Box Pushing
- The thrust beds of required size and designed thickness were cast with M25 concrete. Pin pockets of 0.5m x 0.5m x 0.6m size are provided at suitable spacing for jacking arrangements. The sides of pin pockets are provided with 6mm thick M.S. Plate to take the thrust. The pin pockets are then filled with sand and small layer of screed concrete is placed on them to get smooth surface for casting or Box elements.
- Reference line pillars and TBMs are fixed on the approach to control alignment and level while pushing.
- One layer of plastic sheet is spread on the thrust bed where the box is cast. A layer of grease is applied on it and again one mere layer of plastic sheet is kept. Box elements are cast on this, so that friction is reduced while pushing.
- Entire box concreting done with RMC during nights only since the site is in the heart of the city. The top of the box was painted with epoxy paint after casting to reduce friction.
- With in the box excavation was done with excavator. The excavated earth was lifted by winches and stacked during the day time. The same was transported out during nights. Hard granite rock was met with at bottom layer and also some big boulders at several locations. The same was removed using pavement breakers.
- Initially two elements were cast on both thrust beds. After pushing on element, the element from the other bed was side slewed to maintain continuity of pushing.
- Pushing was done with the help of hydraulic jacks.
- All the S & T cables were protected before pushing.
- Sufficient ballast was unloaded with the help of division before taking up the pushing.
Additional constraints at this site
- The approach roads were not ready. There is a difference of 5 m from existing road level to box bottom. So the excavated earth has to be lifted to Road level as trucks cannot go, since there is no space even for ramp of Fathenagar side.
- This is a heavily built up city area. All transportation has to be done during nights only.
- Very limited area available for the work and stacking of materials.
- Hard Granite rock has been met at bottom of box which slowed down rate of pushing.
- Seepage of drainage water from adjoining areas
General safety precautions taken at site
- Round the clock watch man posted to ensure safety of trains.
- One P. way gang with experienced supervisor kept on track to attend any track disturbance during pushing.
- 9000 Nos. of filled ballast, sand and moorum bags kept at site.
- Ensuring cutting edge always buried in the earth.
- Alignment and level of box checked daily. Any correction required was immediately carried out in the next push by suitably adjusting the pressure in the jacks and by ensuring proper bottom level of excavation.
- Jacking operation stopped while passing a train.
- Track drainage water is diverted.
- Drag sheet arrangement – strengthened.
- Fixing of cutting edge strengthened
Additional safety measures taken at this site
- Second cutting edge: As the size of the box is large, based on the past experience a second cutting edge has been provided at 2m below the top cutting edge and both are interconnected with stiffener plates. This helped in supporting the formation / slope in case of soft soils and emergencies.
- Insertion of rails between sleepers before hand: To take care of any local collapse of formation ahead of cutting edge the running track was supported with cross rails in between the sleepers. One end of these rails was supported on the box and the other end on the formation with the help of wooden blocks. This will help in immediate transfer of load from the running rails to formation in case of any local sinking under the sleepers , while passing of the trains.
- Use of Turfers & Jacks: While pushing the box, there may be disturbance to the track alignment and level. The disturbance in alignment was minimized by the use of turfers & jacks duly applying force in opposite direction.
- Use of channel pieces on rails: While pushing, the track gets lifted up. The running rails can be quickly supported by placing channel pieces of different sizes on the pre-placed rails between sleepers and the trains can be allowed before full attention to the track.
- Applying grease to drag sheets: The friction between the drag sheets and the box can be reduced by applying grease to the drag sheets at the point of drag sheet rolls.
Problems encountered while pushing
- Collapse of over burden ahead of cutting edge: While pushing the second segment a cavity of 0.6m x 0.6m was formed under down line ahead of cutting edge at 13.30 hours on the day due to presence of sand pockets under the track. This had increased to 9m x 3m by 18.00 hours. The track was immediately supported with additional rails and ISMB’s through out the length and moorum and sand bags were provided over the intermediate cutting edge and top cutting edge. ISMBs & channels were driven in to formation on one end and rested on the cutting edge on the other end. Then sand bags were placed on these beams. Box pushing was continued without removing these ISMBs since they were simply resting on the cutting edge. SR of 10 Kmph imposed on down line and the trains were passed safely without any detention. SR was relaxed to 20 KMPH on the day. This was possible only with the help of second cutting edge and cross rails placed in advance.
- Shearing of drag sheets: This may be due to restricted movement of drag sheets which are pressed between cutting edge and soil of the formation, pressing against boulders present in the formation, not able to withstand the forces developed during pushing etc.
Conclusion
- Various unexpected situations are likely to occur during the box pushing operations. Since the safety of running trains is directly affected, proper planning and implementation is essential for smooth completion of work. Advance analysis of site, likely problem that may arise and planning to tackle the same will help the executive for speedy safe completion of the work.
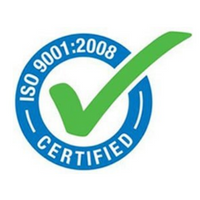
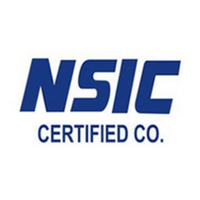
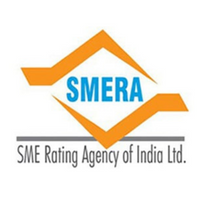
Do you have any requirement and want to discuss?